Аргоновый поддув при сварке нержавейки: как делать качественные заглушки для поддува и варить корень шва аргоном профессионально
Приветствую вас, коллеги-сварщики!
Я давно ждал момента, когда станет доступен качественный двухкомпонентный силикон, из которого мы сможем самостоятельно отливать заглушки для поддува аргона при сварке TIG. И вот это время настало!
Как это часто бывает в нашей сварочной жизни, нам повезло втройне — почти как с тем самым НДТ-рентгенологом, который акцептировал весь проект, не появившись на площадке ни разу. Редко, но бывает.
А вот и три «подарка» для тех, кто варит нержавеющую сталь аргоном с поддувом:
Термостойкость — силикон выдерживает до 300 °C при кратковременном контакте с горячим металлом. Идеально для сварки корня шва с защитой инертным газом!
Пищевая пригодность — подходит для фармацевтики и пищевой промышленности, где особенно важны качественные сварные швы на трубах из нержавейки и алюминия.
Быстрая полимеризация — заглушка для поддува аргона застывает всего за 24 часа.
Бонусы:
Экономия — материал на одну заглушку DN80 стоит около 1,5 евро. За пару часов вы можете отлить до 5 заглушек!
Брендинг — на силиконовых заглушках можно отлить и свой логотип. Отлично для мастерских и индивидуальных сварщиков!
Готовая форма — мы уже подготовили форму для заливки, её можно скачать и масштабировать под нужный диаметр трубы. Отлично работает при сварке TIG, в среде защитного газа, будь то нержавеющая труба, сплав хрома, или тонкостенная металлическая кромка.
Теперь сварка аргоном с поддувом становится доступной каждому. Контроль сварочного тока, выбор электрода, проволоки и стабильная дуга — это важно. Но без правильной заглушки не получится качественный корень шва, и тут наш проект заглушки из силикона — ваш новый союзник.
Личный опыт и рекомендации
Я сам опробовал весь процесс создания заглушек для поддува и готов поделиться с вами всем, что у меня есть. Взамен прошу лишь репост этой статьи на тематических форумах. Ну и загляните в наш блог — там вы найдете другие интересные штуки, связанные с сваркой с поддувом, которые мы разработали и внедрили в свою организацию.
Форма для заглушек для поддува: STEP/STL 3D-модель
Вот проверенная мною 3D-модель в формате STEP/STL, состоящая из четырех частей. Эта модель предназначена для заглушки для поддува с наружным диаметром 94 мм, что подходит для DN80.
Из такой формы каждые 24 часа получается одна заглушка для поддува DN80. Если вам нужна модель для DN150 (OD 169 мм), масштабирование сделать совсем несложно. Просто измените размеры модели, используя программы вроде Cura или любой другой софт для подготовки 3D-печати.
Пример масштабирования:
- Для диаметра 152 мм масштабируйте модель на 61,7 %.
- Для диаметра 212 мм из 152мм — на 39,7 %.
- Масштабирование нужно производить по всем трем осям координат.
3 D-модель заглушки с внутренним металлическим диском толщиной 1 мм
Обновление: 14 января 2025 года
Несколько человек обратились ко мне с просьбой создать модель для более крупной заглушки с металлическим диском толщиной 1 мм. Такие заглушки часто производятся массово, и вы, скорее всего, уже видели их.
Я рекомендую использовать эту заглушку для труб диаметром от DN 200 до 400 мм.
Я создал модель диаметром 280 мм, используя оригинальную заглушку в качестве основы . Особое внимание было уделено специальному пазу, который упрощает установку металлического диска в центр заглушки. Этот паз расположен только с одной стороны.
Вы можете скачать модель — Purge Dn 250 — 200_STEP
PDF-чертеж — purge plug silicon dn 250
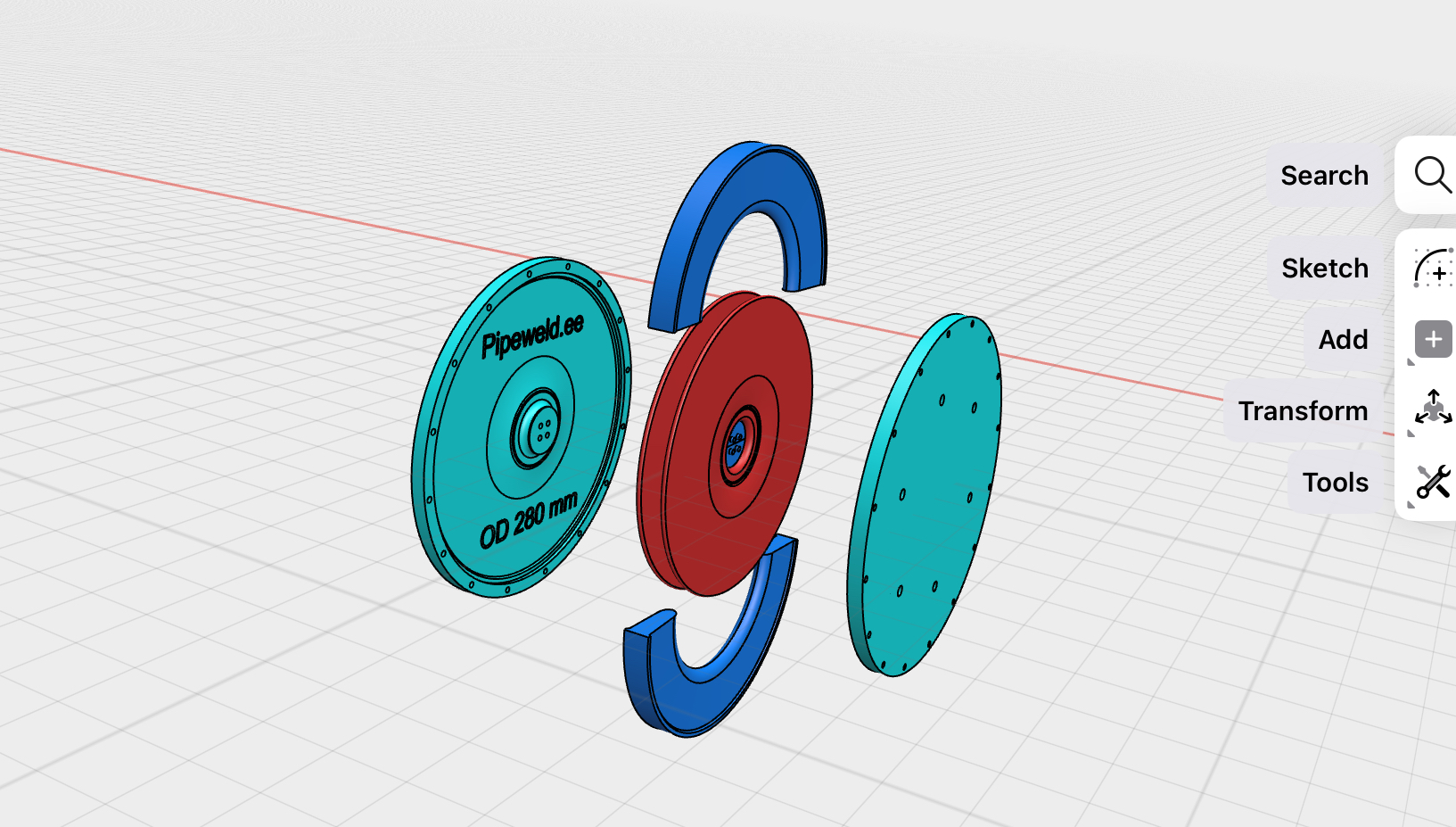
Обновление: 1 февраля 2025 года
Поскольку выяснилось, что при масштабировании моделей пропорционально изменяется и посадочное отверстие в центре заглушки (а оно нам необходимо фиксированного диаметра), я решил выкладывать готовые STL-файлы. Таким образом, вы сможете сразу передавать их на печать без дополнительного масштабирования.
Первая партия заглушек имеет наружный диаметр в диапазоне от 65 до 107 мм.
Скачивай файл, распечатывай и отливай свои заглушки по 1,5 евро за штуку.
- 65 — 15 mm stl file
- 70 — 15 mm stl file
- 75 — 15 mm stl file
- 80 — 15 mm stl file
- 85 — 15 mm stl file
- 90 — 15 mm stl file
- 95 — 15 mm stl file
- 100 — 15 mm stl file
- 107 — 15 mm stl file
Мы обсудили и пришли к выводу, что в заглушках с наружным диаметром от 115 мм и больше, где ранее планировалась установка металлического диска (см. выше), можно обойтись без него. Поэтому я выкладываю готовые модели всех диаметров, начиная с 115 мм, и планирую довести их до 400 мм. Теперь вместо диска они зажимаются шайбой с гайкой, а отверстие (20 мм) предусмотрено во всех заглушках, перечисленных ниже.
Для крепления этих дисков вы покупаете вот таки крепления в Китае
- 115 — 20 mm stl file
- 125 — 20 mm stl file
- 137 — 20 mm stl file
- 145 — 20 mm stk file
- 160 — 20 mm stl file
- 167 — 20 mm stl file
- 175 — 20 mm stl file
- 190 — 20 mm stl file
- 210 — 20 mm stl file
- 230 — 20 mm stl file
- 250 — 20 mm stl flle
- 270 — 20 mm stl file
- 280 — 20 mm stl file
Обновления 04/02/25
3D модель формы для литья силиконовых заглушек диаметром 35–55 мм с отверстием 15 мм в центре.
Скачивай файл, распечатывай и отливай свои заглушки по 1,5 евро за штуку.
- 55 — 15 mm stl file
- 50 — 15 mm stl file
- 45 — 15 mm stl file
- 40 — 15 mm stl file
- 35 — 15 mm stl file
- 30 — 15 mm stl file
Какой силикон выбрать для заглушек для поддува?
Я рекомендую использовать только платиновый силикон: он менее капризен, стерилен, не имеет запаха и очень удобен в работе.
- Твердость: для заглушек для поддува оптимальна твердость по Шору от 60 и выше. Шор 20 — слишком мягкий, примерно как обычный силикон, а нам нужно втрое тверже.
- Пропорции: для правильного смешивания компонентов вам понадобятся весы с точностью до 1–2 граммов.
Процесс заливки силикона для заглушек для поддува
- Смешивание: тщательно перемешивайте силикон не менее 5 минут. Соберите 3D-напечатанную форму, закрепив детали болтами.
- Вакуум: если возможно, поместите смешанный силикон в вакуумную камеру для удаления пузырей. Если вакуумной камеры нет, выбирайте силикон с повышенной текучестью и свойствами самодегазации.
- Заливка: используйте большой медицинский шприц (100+ мл) для точной заливки. Для DN80 потребуется 40 граммов силикона.
Извлечение заглушек для поддува
Через 24 часа можно разобрать форму и извлечь диск для поддува. Однако не используйте его сразу — он может оставаться липким. Дайте ему отлежаться пару дней вне формы, чтобы поверхность полностью застыла.
Что вам нужно купить для удобной работы и хорошего результата:
- Найдите, где можно распечатать 3D-модель, и попросите там масштабировать модель до нужных диаметров.
- Купите платиновый силикон с твердостью по Шору 60.
- Приобретите прижимные болты (8 штук). Диаметр будет изменяться в зависимости от масштабирования. Для ДУ 80 подходят болты М5.
- Купите шприц объемом 100 мл.
- Подготовьте мерную посуду и емкость для смешивания.
Вывод: силиконовая заглушка — ключ к профессиональной сварке нержавеющих труб с поддувом
В процессе аргонодуговой сварки TIG, особенно при работе с нержавейкой, важнейшим фактором, влияющим на качество шва, является правильная организация системы поддува. Поддув аргона внутрь трубы необходим для формирования обратной стороны шва, защиты металла от контакта с кислородом и предотвращения коррозии сварного соединения в будущем. Именно поэтому технология сварки аргоном с поддувом остаётся стандартом при работе с нержавеющими сталями.
В рамках нашей практики мы разработали силиконовую заглушку, которую можно отливать самостоятельно, не прибегая к дорогим и недоступным решениям. Такая заглушка позволяет сварщику:
-
удерживать нужное давление защитного газа,
-
обеспечить равномерную защиту шва от окисления,
-
и добиться стабильного корня шва при аргонной сварке нержавеющих труб.
Эта разработка подходит как для аргонодуговой сварки TIG, так и для полуавтоматической сварки нержавейки, где требуется поддувом аргона защищать сварочную ванну и зону обратной стороны шва.
Мы учли особенности сварки в среде защитного газа, где аргон подаётся через шланг и регулируется через клапан выхода защитного газа. Силиконовая заглушка от нашей команды идеально сочетается с сварочным оборудованием, горелками, и присадочным материалом, обеспечивая качественное выполнение сварных соединений.
Такое решение особенно актуально при оказании услуг аргонной сварки: заказчик получает не только чистый, прочный сварной шов, но и уверенность в том, что металл защищён в среде аргона от всех внешних воздействий.
Варить без поддува в большинстве случаев — значит жертвовать качеством. С нашей заглушкой это в прошлом.
Мы рады предложить коллегам по цеху готовую форму, расходные материалы и полную инструкцию по созданию своей системы поддува. Это — шаг к более профессиональному подходу и развитию навыков в сфере аргонодуговой сварки, будь то TIG или ручная дуговая сварка с присадкой, сварочной проволокой или электродом.
Развитие проекта. Изменения от 10.03.2025
Коллеги, стоит признать, что дьявол кроется в деталях. Этот проект поглотил меня, и вместе с моим 13-летним сыном мы начали его развивать, тестировать и дорабатывать. Оказалось, что он значительно интереснее, чем я предполагал в самом начале.
Основные выводы и принятые решения
-
Проблема с выбором силикона
С вашей помощью мы убедились, что найти силикон с твердостью 60 – задача не из легких. Поэтому было принято решение отказаться от этой идеи и адаптировать проект под более доступные виды силикона.
Решение: Мы разработали четыре новые модели заглушек, отлив их самостоятельно. Выяснилось, что предложенный дизайн прекрасно подходит для силиконов с твердостью 20 и 40. Сейчас мы ждем обратной связи, чтобы адаптировать модели под различные диаметры. -
Масштабирование деталей
К сожалению, масштабирование деталей имеет свои ограничения.
Решение: Каждый дизайн придется разрабатывать отдельно для каждого диаметра. Это не пугает нас, главное – определить, какой именно дизайн подходит для того или иного диаметра. В связи с этим мы предлагаем на рассмотрение три варианта дизайна. По плану:- Модель 40 мм будет адаптирована для диаметров от 40 до 65 мм.
- Модель 75 – для диаметров от 65 до 115 мм.
- Модель 115, вероятно, рассчитана до 156 мм, а модель 115+ планируется для диаметров от 156 до 290 мм.
-
Экономия силикона
Вам необходимо знать, какой объем силикона требуется для изготовления каждой заглушки. Теперь эта информация будет отражаться в названиях файлов. -
Использование обтяжных болтов
Практический опыт показал, что обтяжные болты для форм не требуются – по крайней мере, для моделей с диаметрами от 40 до 115 мм (более крупные образцы мы пока не тестировали). Форма в сборе оказывается достаточно прочной, однако рекомендуется иметь под рукой две небольшие струбцины. -
Заливка силикона в форму
Чем выше твердость силикона, тем ниже его вязкость, что затрудняет процесс заливки в форму. Необходимо усовершенствовать технологию заливки/инъекции.
Решение: Мы приобрели вакуумную камеру стоимостью 150 евро. После смешивания силикона в стакане помещаем его в камеру на 15 минут при отрицательном давлении (–1 бар). Затем, аккуратно, чтобы не захватить воздух, с помощью шприца проводим инъекцию в форму в два этапа: сначала заполняем 75% объема, даем силикон отстояться в течение 3 минут, а затем добавляем оставшиеся 25%.
Если у вас отсутствует вакуумная камера, её можно изготовить самостоятельно – подробности см. тут — https://www.youtube.com/watch?v=xLj6YU97pjQ. Кроме того, можно вылить силикон из стакана на тарелку, что значительно увеличит площадь поверхности и уменьшит толщину слоя. Это позволит воздушным пузырям быстрее выйти на поверхность. -
Формат файлов
Оказалось, что не всем удобно работать с файлами в текущем формате. Мы учли этот момент и уже исправили данный недостаток.
Заключение
Также мы разместили короткие видеоролики о развитии проекта в социальных сетях. Мы будем признательны за ваше внимание и взаимодействие с ними.
Будем рады вашим отзывам и предложениям для дальнейшего совершенствования проекта!
https://vm.tiktok.com/ZNdeV9UNq/
https://vm.tiktok.com/ZNdeVaukm/
https://vm.tiktok.com/ZNdeVDH9T/
Новые Модели можно скачать тут
Огромное спасибо за такую очень нужную разработку!